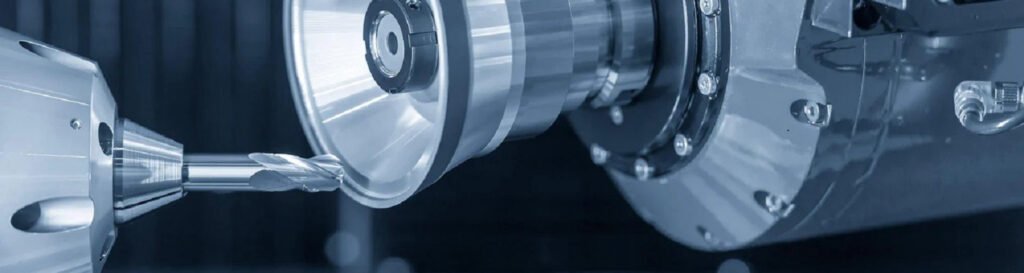
Recondition machining tools
when (and how) is right doing it
In many companies, used solid carbide tools are scrapped as soon as they become worn or damaged.Still, this isn’t the only option available.
Today you can extend the life of your tools by reconditioning them and this helps you to reduce their initial cost. Have you ever considered the possibility of regrinding and refurbishing your tools before?
What does tool reconditioning consist of?
Reconditioning is a process of “rejuvenating” existing solid carbide tools, such as drills, reamers and cutters.
Good quality cutting tools are not cheap and tend to wear out over time. The cost of replacing them is often high, especially for smaller mechanical workshops with limited budgets.
What are the benefits of tool reconditioning?
The budget you invest in new tools is often an economic investment that should not be underestimated.
For this it is essential to find a way to offset the initial purchase cost. A good tool reconditioning program enables companies to meet rigorous standards and compete in the market while delivering quality and cost-effective products.
Some of the benefits:
>>>reduce inventory costs
>>>increase your competitiveness on the market
>>>avoid wasting material
>>>increase corporate sustainability
So, to summarize, it is possible to give new life to worn tools, allowing companies to increase their productivity and save money by avoiding unnecessary purchases.
Tool reconditioning program
How do I know if it’s time to refurbish my tools?
In addition to the obvious signs of blunt and rounded cutting edges, there are some details that machine operators should be able to recognize, in order to understand whether a tool needs to be refurbished or not. Here are some examples:
>>>Decrease in cutting capacity
>>>Higher machine and spindle loads
>>>Worst surface finishes
>>>Chip shape and size
When is it not recommended to recondition tools?
If the cutting edges of the tool are heavily worn and damaged, it is not always possible to reconstruct the correct geometry and respect the dimensional tolerances.
Therefore, it is essential for the user to pay attention to the wear levels and define the correct cutting screws, in order to then be able to take advantage of the advantages of reconditioning seen above.
Thanks to the processes of reconstruction and re-sharpening of the cutting edges and reapplication of the coating, we restore the geometry of the tool and the coating to the original characteristics.
